More yarn ready for the sale. I have been spinning every day to increase what I have for sale and display. The browns in this bunch all came from walnut hulls! The greys are all natural. I remember having sheep in several beautiful shades of silver, brown and white. Oh, I do miss them.
Today, I will be packing up the wheel. Time to get busy marking all the new yarn. I am really excited about the sale in Wheaton, MN this weekend. There will be seventy
vendors in all. I may have to do a little shopping while I am there....
Besides the yarn, I will have a few books, patterns and a loom for sale. Also, there will be handmade paper items such as bowls, cards and bookmarks, Origami and 'Keeper Boxes'. I will be posting some photos of these after the sale. I plan to take pictures of some of the other booths as well. Watch for these next week.
October 30, 2013
October 18, 2013
Getting Ready for the Sales!
I have been working hard lately getting things ready for the upcoming sales. I have to measure, weigh, and tag each skein of yarn to be sold. Then, I have to go back and price everything. I am hoping to get everything entered into this site and my Etsy site. This is one if the racks I will be using for display.
All of the yarns I sell are farm yarns. They are all raised on my farm or other amall farms and either processed by hand on the farm or in small mills that maintain the individuality of each fleece. All are wool, or a blend of wool and other natural fibers. Each skein is hand spun. Colors are either the actual color from the animal, or dyed by hand with natural dyes, many made from local plants. Some are blended by hand before spinning to produce variegated skeins and more colors. This make every skein unique and provides the chance to work with and create individual, one of a kind projects. Whether the yarns are used alone or combined with other yarn, the end result is totally unique.
I also have been busy developing a class for after the first of the year. I have been asked to present a natural dyeing class at Dakota Fiber Mill near Kindred. We have decided to wait until after the holidays to do the class. I am planning on using several different dye stuffs that don't have too bad a smell...since we will be inside! I also will avoid any really nasty mordants. I think it will be a fun and informative day. I will be posting more information on dates, times, cost, etc. as things come together.
All of the yarns I sell are farm yarns. They are all raised on my farm or other amall farms and either processed by hand on the farm or in small mills that maintain the individuality of each fleece. All are wool, or a blend of wool and other natural fibers. Each skein is hand spun. Colors are either the actual color from the animal, or dyed by hand with natural dyes, many made from local plants. Some are blended by hand before spinning to produce variegated skeins and more colors. This make every skein unique and provides the chance to work with and create individual, one of a kind projects. Whether the yarns are used alone or combined with other yarn, the end result is totally unique.
I also have been busy developing a class for after the first of the year. I have been asked to present a natural dyeing class at Dakota Fiber Mill near Kindred. We have decided to wait until after the holidays to do the class. I am planning on using several different dye stuffs that don't have too bad a smell...since we will be inside! I also will avoid any really nasty mordants. I think it will be a fun and informative day. I will be posting more information on dates, times, cost, etc. as things come together.
October 15, 2013
Sorry for being a no-show lately....
Sorry that I haven't been posting much lately. I have been really busy. I went to an art crawl a week ago. I was out of town for four days. I have two shows/sales coming up, one in Wheaton, MN on November 2nd, and one in Battle Lake, MN on December 7th. I have been very busy dyeing, blending and spinning yarn for those. I will try to post more pictures soon of some of the yarns that will be for sale soon. This will be one of the skeins for sale.
October 2, 2013
Say Hello to the Blending Board
As much as I enjoy blending colors on a drum carder, I am excited to try another method. I happened to run across a new toy I have to have...a blending board. A blending board is sort of like a flat drum carder. It is used just for blending and not carding. It is best used with roving, locks, sliver, things that are already carded or ready to spin. You don't want to put your fiber on a blending board and then blend it into mud! The idea is to gently blend the fibers together. You decided when they are blended enough.
With a blending board, you have more control over the finished product than you do with a drum. It is much easier to make stripes, repeats, and patterned yarns. You can still add threads, locks, tinsel, and anything else you want to spin into the yarn.
There are several blending boards available. Clemes and Clemes has a really nice one. Moonsong Fiberworks and Paradise Fibers are a couple others. If you look, you will find them. The thing is, they are pretty expensive. They range in price from about $165 to $230 dollars. I decided that I couldn't spend that on another spinning toy right now, so I built one myself.
These are the supplies I bought. I had purchased a piece of carding cloth from Naturafiberyarns on Etsy. The size of the cloth was 11 7//8" wide by 12" long with 72 tpi. It only took about a week to get the cloth. I went looking for a cutting board or shelf board that it would fit on, but couldn't find the right size. I finally found a piece of Aspen that was 15" by 36" and 3/4" thick. It was edge glued for extra strength, and was much lighter than some of the cutting boards I looked at.This seemed like it would work well for my purpose.
The hardware, board and glue were all purchased at a local hardware store. I also picked up a thumb screw, two washers, a T-nut, and a can of 3M 77spray adhesive. (Please, see the comments at the end of this post regarding attaching the carding cloth. I have been made aware tht the cloth should be edge stapled, but never glued).
I measured the board out to be just slightly wider than the cloth and
about 4 inches longer. I wanted to have a handle at the top. My husband
cut the board for me and also drilled out the handle. I sanded it all
down well so there were no sharp edges or lose wood. Then I put a couple coats of clear polyurethane on it to help protect it. I decided where
the keel would sit on the bottom, drilled a hole and pounded in the
t-nut. Then I had my husband cut the board for the keel.
A blending board has a piece called a keel on the bottom of the board. When you are going to use the board, you use the thumb screw to attach the keel to the bottom. Attach it tightly, but no so tight that it won't turn. When you are blending, put the keel between your knees and swivel the board to an angle that is comfortable for you. This is a really nice feature. You don't have to work at weird angles and it makes things much more enjoyable.
When loading the board, simple pull the fiber through the teeth to apply it where you want it. You can make measured, repeating stripes or just add fiber randomly. If you want a certain color or kind of fiber in a particular spot, place it there. You can make batts that are all the same or not, depending on what you want.
With a blending board, you have more control over the finished product than you do with a drum. It is much easier to make stripes, repeats, and patterned yarns. You can still add threads, locks, tinsel, and anything else you want to spin into the yarn.
There are several blending boards available. Clemes and Clemes has a really nice one. Moonsong Fiberworks and Paradise Fibers are a couple others. If you look, you will find them. The thing is, they are pretty expensive. They range in price from about $165 to $230 dollars. I decided that I couldn't spend that on another spinning toy right now, so I built one myself.
The hardware, board and glue were all purchased at a local hardware store. I also picked up a thumb screw, two washers, a T-nut, and a can of 3M 77spray adhesive. (Please, see the comments at the end of this post regarding attaching the carding cloth. I have been made aware tht the cloth should be edge stapled, but never glued).
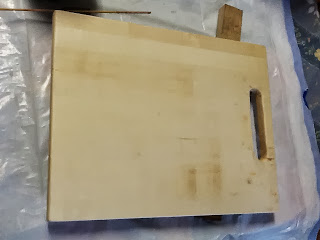
A blending board has a piece called a keel on the bottom of the board. When you are going to use the board, you use the thumb screw to attach the keel to the bottom. Attach it tightly, but no so tight that it won't turn. When you are blending, put the keel between your knees and swivel the board to an angle that is comfortable for you. This is a really nice feature. You don't have to work at weird angles and it makes things much more enjoyable.
When loading the board, simple pull the fiber through the teeth to apply it where you want it. You can make measured, repeating stripes or just add fiber randomly. If you want a certain color or kind of fiber in a particular spot, place it there. You can make batts that are all the same or not, depending on what you want.
October 1, 2013
Dyeing Wool with Black Walnuts
I love this time of the year. The days are clear, dry, and warm (high 60's-low 70's), but not hot. Bugs are not as bothersome as in summer. Colors are starting to pop on the trees and in the hedgerows. My kind of weather. I wish fall could last for many months. It is perfect for dyeing on the deck. I can have a fire, bring my wheel outside and cook away! My husband, Clint, cut lots more firewood for me on Sunday. I am currently spinning a wool/mohair fiber that I dyed earlier. The colors are blended together on a drum carder using wool dyed with lichen, mullein, and onion skins.
I found a great source for Black Walnuts Saturday. I found a tree that was dropping walnuts like rain! You have to accept getting hit in the head a few times in payment to the tree for taking her fruit, but it was well worth the trouble (and discomfort...). Within about 15 minutes I had collected more than enough walnuts to use for a class will be teaching as well as to dye plenty of wool for myself. I got them home and stowed them safely away for the night. The next day, I got started.
If you wish to dye with the whole thing, nut and hull, you can place them in a dye pot right away. Make a layer on the bottom of the pot and cover with water. Boil for a couple hours, watching and adding water as needed. then cool, drain, and there is your dye bath. Add enough extra water to this to allow your wool/yarn to move freely in the pot. You don't even have to mordant the wool for dyeing with walnuts, although, you may be able to create different colors if you do.
Walnuts are hard to store in the hulls. They have to be carefully dried to prevent them from developing mold. Also, they need to be constantly guarded from squirrels and other critters that consider them groceries. Because of this, I prefer to use dried walnut hulls. This also allows me to boil up a dye bath any time of year. Hulling the walnuts can be done quite easily with an old hammer, or a stone, and a board. Simply hit the nuts with the hammer and peel the nut out of the hull. The hull is what is then used to dye with.
I filled a dye pot about half full of walnut hulls and covered them with water. I added more water to bring the level to about 3/4 full. I boiled these for two hours. After that time, I removed the pot from the heat and let the hulls steep over night. I also mordanted one pound of wool with alum and Cream of Tarter in the usual way, simmering for an hour and then cooling in the liquid.
I had some Chicken of the Woods that I wanted to try dyeing with. For this, I mordanted half a pound of wool in a 10% ammonia mordant. I let this sit in the mordant for several hours. I did not heat it. I removed the wool from the mordant and rinsed it well with clear water. I then added the wool to the dye bath I had made earlier by boiling the mushrooms in water and straining. I was disappointed with the result, there was little color change. I let this sit over night with no improvement. I rinsed the wool with clear water and decided to over dye it in the walnut dye bath to see how the ammonia mordant would react.
After soaking over night, I strained the dye liquid from the walnut hulls. I decided to add the wool with the ammonia mordant first. I placed the wool in the dye pot and simmered this for a couple of hours. Then I left it to steep and cool. The result was a warm, rich brown. The wool was wonderfully soft. I was concerned with the use of ammonia, but it really doesn't hurt the wool.
I found a great source for Black Walnuts Saturday. I found a tree that was dropping walnuts like rain! You have to accept getting hit in the head a few times in payment to the tree for taking her fruit, but it was well worth the trouble (and discomfort...). Within about 15 minutes I had collected more than enough walnuts to use for a class will be teaching as well as to dye plenty of wool for myself. I got them home and stowed them safely away for the night. The next day, I got started.
If you wish to dye with the whole thing, nut and hull, you can place them in a dye pot right away. Make a layer on the bottom of the pot and cover with water. Boil for a couple hours, watching and adding water as needed. then cool, drain, and there is your dye bath. Add enough extra water to this to allow your wool/yarn to move freely in the pot. You don't even have to mordant the wool for dyeing with walnuts, although, you may be able to create different colors if you do.
Walnuts are hard to store in the hulls. They have to be carefully dried to prevent them from developing mold. Also, they need to be constantly guarded from squirrels and other critters that consider them groceries. Because of this, I prefer to use dried walnut hulls. This also allows me to boil up a dye bath any time of year. Hulling the walnuts can be done quite easily with an old hammer, or a stone, and a board. Simply hit the nuts with the hammer and peel the nut out of the hull. The hull is what is then used to dye with.
I filled a dye pot about half full of walnut hulls and covered them with water. I added more water to bring the level to about 3/4 full. I boiled these for two hours. After that time, I removed the pot from the heat and let the hulls steep over night. I also mordanted one pound of wool with alum and Cream of Tarter in the usual way, simmering for an hour and then cooling in the liquid.
I had some Chicken of the Woods that I wanted to try dyeing with. For this, I mordanted half a pound of wool in a 10% ammonia mordant. I let this sit in the mordant for several hours. I did not heat it. I removed the wool from the mordant and rinsed it well with clear water. I then added the wool to the dye bath I had made earlier by boiling the mushrooms in water and straining. I was disappointed with the result, there was little color change. I let this sit over night with no improvement. I rinsed the wool with clear water and decided to over dye it in the walnut dye bath to see how the ammonia mordant would react.
After soaking over night, I strained the dye liquid from the walnut hulls. I decided to add the wool with the ammonia mordant first. I placed the wool in the dye pot and simmered this for a couple of hours. Then I left it to steep and cool. The result was a warm, rich brown. The wool was wonderfully soft. I was concerned with the use of ammonia, but it really doesn't hurt the wool.
I then rinsed the alum mordanted wool and cooled the dyebath so I could add the new wool. I let that simmer for two hours as well. I left it to cool and steep overnight. The next day, I removed it from the pot and washed it with Eucalan Wool Wash. The color is basically the same as the wool mordanted with ammonia, but a bit lighter and more golden.
(The two darker pieces on the end are done with ammonia).
I have the walnuts used for this dye bath soaking in more water. I plan to leave them for a few days and then heat them and let them cool again to see how much color they will produce.I am not sure whether the lighter shade in the second bath is due to the mordant or just that it is the second run in the dye bath. I have a lot more walnuts, wool, mordant, and time to see what colors I can create!
Subscribe to:
Posts (Atom)